Foam Extrusion Seminar, 3 day Seminar
May 12-14, 2014
Sheraton Sand Key Resort
Clearwater Beach, FL
Phone: 727-595-1611
by Chris Rauwendaal and James Throne
Printable Outline
About the Seminar
This seminar covers important materials, equipment, and process issues of foam extrusion in a comprehensive fashion.
The objectives of this seminar are:
- to teach the basic principles of foam extrusion
- to demonstrate the application of these principles to material selection, equipment selection, setting process conditions, and troubleshooting
- to provide information that processors can take back to the plant to improve production and product quality
What the attendees will learn:
- the basic principles of foamed polymers: mechanical properties, characteristic of foamable polymers, additives, foaming agents, and rheology of gas-laden melts
- foaming agents: endothermic versus exothermic, nucleation, compatibility, open cell foams, natural fiber foam composites, and foaming agent chemistry
- extrusion equipment for foam extrusion: single screw extruders, twin screw extruders, tandem extrusion systems, screw and die design for foam extrusion, high versus low density products
- troubleshooting foam extrusion problems: tools for troubleshooting, extrusion instabilities, irregular cell structure, corrugations and striations,poor melt strength, die freeze-off, and case studies
Who should attend:
- Design engineers
- Process engineers and manufacturing engineers
- Manufacturing managers
- Production supervisors/managers
- Technical service personnel
Testimonial from previous Seminars
Course Description
|
Basic Principles
• Mechanical properties of foams
Std time behavior: stiffness, strength
Long time behavior: creep, fatigue
Short time behavior: impact
• Foamable polymers
Morphological characteristics
Characteristics of important resins
• Additives
• Cell stabilizers
• Other agents
• Nucleating agents
• Foaming agents
• Chemical : exo- and endo-thermics
Physical: atmospheric, hydrocarbons, HCFCs
Solubility and diffusivity
• Rheology of gas-laden melts
Bubble mechanics
Why does a foam stop growing?
And why does it shrink?
Open-celled foams
Foaming Agents
• Natural Fiber Foam Composites
Polymer Structures
Process of Manufacturing
Pressurization
Cooling and Mixing
Role of Cellular Structures
Fine Cellular Structure
Chemistry of the Foaming Agent
Die Configuration and Extrusion
• Foaming Agent Process and Perfor-
mance
Introduction
Foaming Agent Technologies
Endothermic & Exothermic
Foaming Agents
Gases & Nucleation
Elastomeric Foam Design
What 's happening in the Barrel?
Blowing Agent Compatibility
Blowing Agent Process
Properties of Foam Articles
Process Improvement using CO2
Open Cell Foam
Foaming agent studies
Foaming agents in IM & Extrusion
New Equipment Technologies
|
Course Description (continued)
|
Hardware
• Twin vs. single screw extruders
• Single- vs. two-stage process
• Screw design for foam extrusion
• Melt temperature distribution
• Die design for foam extrusion
• High vs. low density foam products
• Free foaming method
• Constrained foaming method
• Microcellular foam extrusion
• Coextrusion
Thermoformability of Low-Density Thin-Gauge Sheet
• Material-Specific Die Design for Thin- Gauge Sheet
• Temperature-Dependent Internal Cell Gas Pressure During Cooling
• The Role of Sheet Aging Prior to Ther- moforming
• Factors Influencing Secondary Foam Expansion During Reheating
• Internal Cell Gas Pressure
• Temperature-Dependent Tensile Modulus
• Processing Factors Influencing Cata-
strophic Cell Collapse
Troubleshooting
• Requirements
• Tools for troubleshooting
• Systematic troubleshooting
• Extrusion instabilities
Frequency of instability
Functional instabilities
Solving extrusion instabilities
• Computer aided troubleshooting
• Case studies
Wear problems
Mixing problems
Irregular cell structure
Dimensional variation
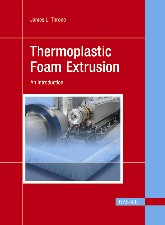
Thermoplastic Foam Extrusion by James L. Throne is available from Hanser Publications with a discount code you receive when registration is confirmed..
Books authored by Chris Rauwendaal are available from Hanser Publications with any seminar registration for a discounted price with a code you receive when registration is confirmed :
The following book is available from REE
- Mixing in Polymer Processing
|
About the Instructor:
Dr. Chris Rauwendaal has been a top seminar instructor for more than 25 years. He has taught with SPE, UWM & UC Berkeley & teaches many in-house courses. He is a well known plastics author. Chris has 30+ years experience in the plastics industry. His experience is in a wide range of extrusion operations, including fiber spinning, film, sheet, tubing, medical tubing & profile extrusion, coextrusion, and reactive extrusion. He has worked on both practical and theoretical problems such as screw & die design, troubleshooting, modeling and computer simulation, material analysis, failure analysis, etc. Chris has authored 6 books on extrusion and related fields.
Since 1990 he has been President of Rauwendaal Extrusion Engineering, Inc., a company that provides custom extruder screws and other extrusion hardware, training programs, engineering & expert witness services to the plastic industry. With screw design as his specialty, over the past 5 years REE had developed patented technologies in the following areas:
• Elongational Mixing Devices
• Mixing non-return valves
• Single screw compounding extruder
• Cooling screws for foam extrusion
For registration contact: chris@rauwendaal.com
For seminar content contact: chris@rauwendaal.com